業務変革の支援をするIT企業のマクニカは、製造業向けのAI(人工知能)導入などのDX(デジタルトランスフォーメーション)推進で最もハードルが高いのは導入初期にあると見る。改革の推進者と製造現場、経営といった組織内で課題を共通認識し、疲弊せずにデータを活用した業務改革をする秘訣を聞いた。
「DX(デジタルトランスフォーメーション)が上手く行かないのは、技術が悪いわけではない」。マクニカの阿部幸太インダストリアルソリューション事業部長は、300以上の業務改革支援を通じてそう断言する。「業務プロセスを変えるのが一番難しい。いかに現場を巻き込めるかがDXを成功させるポイントだ」(同)。
製造業によるAI(人工知能)活用などによるDX推進では、製造現場の業務プロセス変更が伴う。多くの企業で共通の課題とされている「多品種少量短納期に対応できるようにする」という目的において、この業務プロセスの変更がボトルネックとなるケースが多い。関連する部署や参照するデータが多岐にわたるためである(阿部氏)。よって、人手不足の中で工夫しながら製造を進める現場にとっては、こうしたプロジェクトの協力が一時的に負荷を高めてしまう。DXの狙いや目的が共通認識できていないと、導入しても使われなくなってしまうのだ。
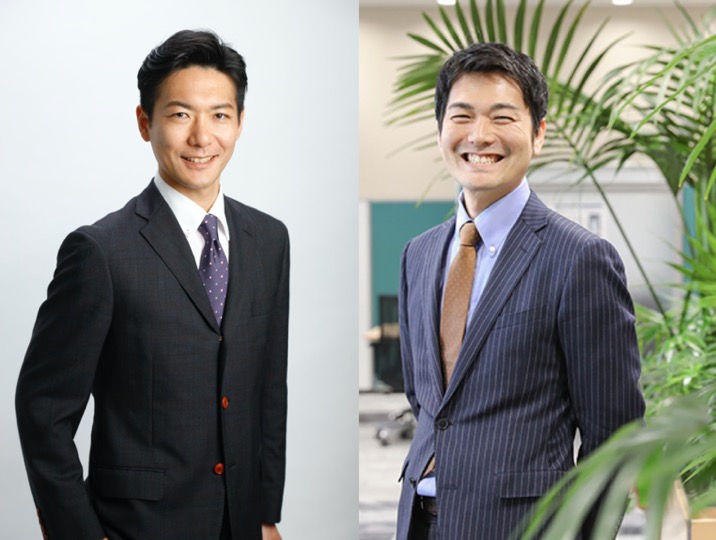
(左より)株式会社マクニカ AI Resear ch & Innovat ion Hub プリンシパル 楠貴弘氏
株式会社マクニカ インダストリアルソリューション事業部 事業部長 阿部幸太氏
よくあるDX推進は5割失敗
こうした課題から、マクニカでは製造業のDX推進を促すサービス群「Digital Synergy Factory.macnica.ai(デジタル・シナジー・ファクトリー・マクニカドットエーアイ)」を4月に打ち出している。「組立工程の可視化」や「外観検査自動化」など、企業の課題別にすぐに導入できる形でモジュールにし、組み合わせて導入できるものだ。狙いは、DXで最も難しいプロジェクトの初期段階を一足飛びに実現することだ。
「こうした、ありがちなDXのプロセスでは、5割以上の企業が途中で力尽きてしまう」。阿部部長は、そういってスモールスタートをコンセプトにした業務変革の進め方を示した。まず、データ活用の効果が高い課題の設定をし、その効果検証をしながらAIの精度を高めるなどデータの使い方を改善。成功体験を基に、別の業務にも同様のデジタル化を水平展開していくというものだ。
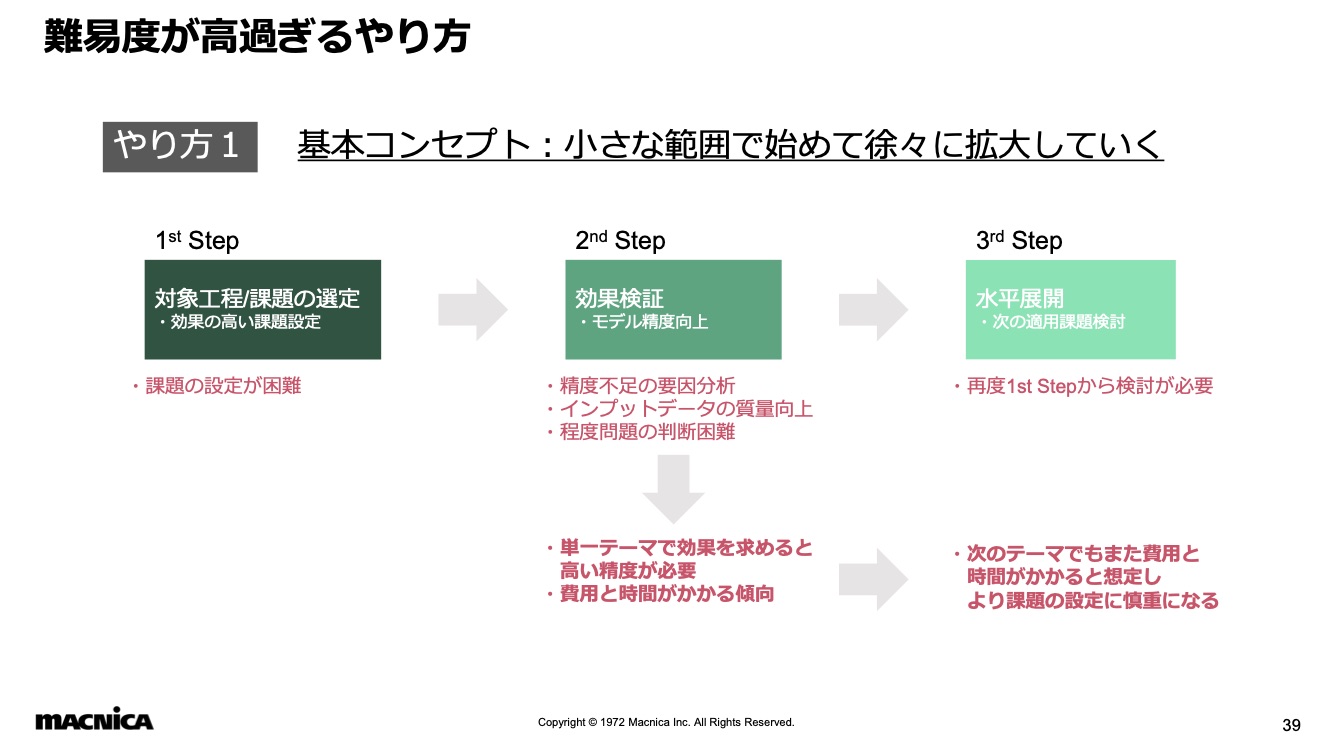
[画像クリックで拡大]
導入初期で半数以上が失敗するというDXの進め方
一見すると良さそうにも見えるDXの進め方だが、「活用するデータの収集を自動化するところからスタートする企業にとって、とても負荷が高い」と阿部部長は指摘する。例えば、最初の「効果がありそうな課題」を設定するのも一苦労だ。どの課題が最も効果が出そうなのか、その調査だけでDX推進の担当者は疲弊してしまう。効果検証でもデータ不足などから思うように精度が出ず、効果が実感しづらいため、製造現場の担当者に理解を得るのも難しくなって水平展開も思うように進みにくいという。
対して、マクニカのデジタル・シナジー・ファクトリーでは、課題の設定に先んじてサービス導入が始まる。精度は7~8割と高く無いものの、工程・工場の全体がどう動いているかを可視化するのが目的だ。こうしたサービスを最初に導入することで、同じデータを基にして経営と現場、DX推進担当者が「何が優先課題か」を議論しやすい。業務のデジタル化を進める納得感が得やすく、現場の業務プロセス変革にも着手しやすい。
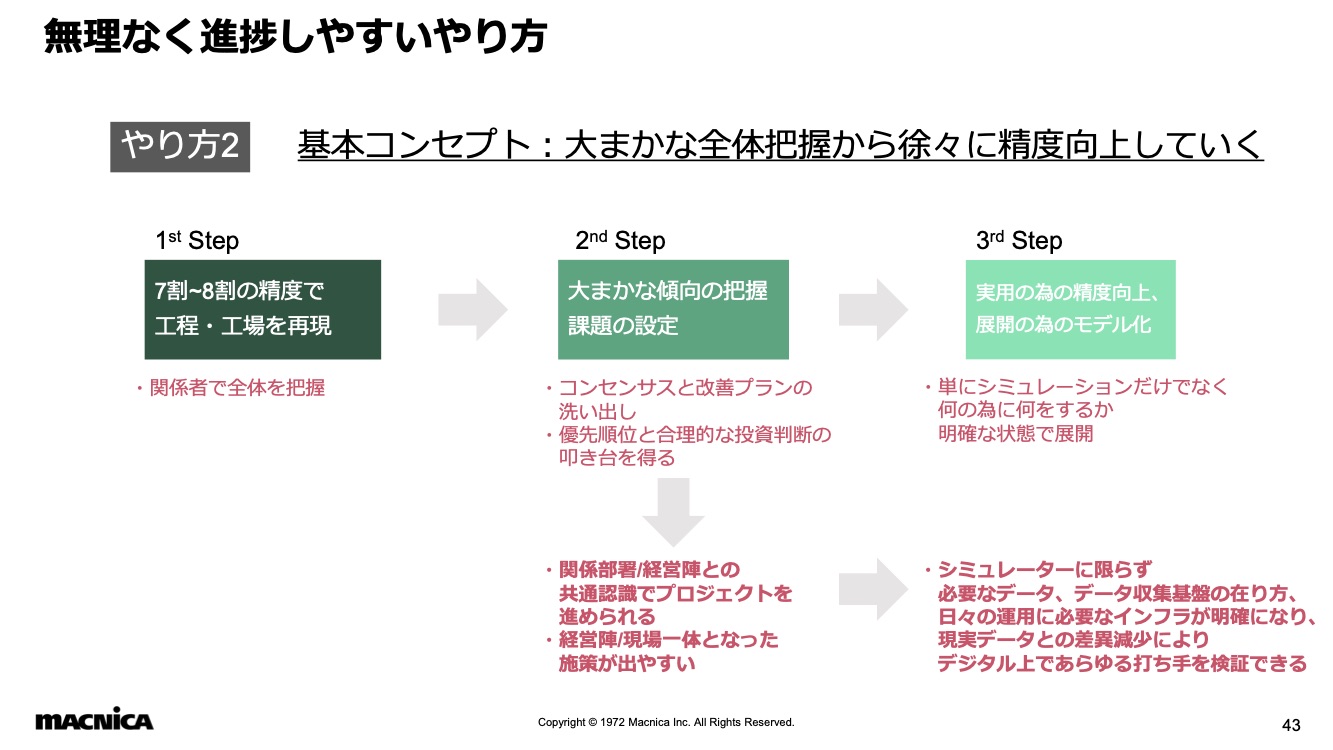
[画像クリックで拡大]
この記事は参考になりましたか?
- この記事の著者
-
広田 望(ヒロタ ノゾム)
物書き、工学学士(応用化学)、理学博士(物理学)
日経BPに入社し、日経コンピュータ記者や日経ビジネス記者を経験。2019年6月にAIベンチャーへ転職し、深層学習を組み込んだサービス開発や人材開発に従事した。※プロフィールは、執筆時点、または直近の記事の寄稿時点での内容です
この記事は参考になりましたか?
この記事をシェア