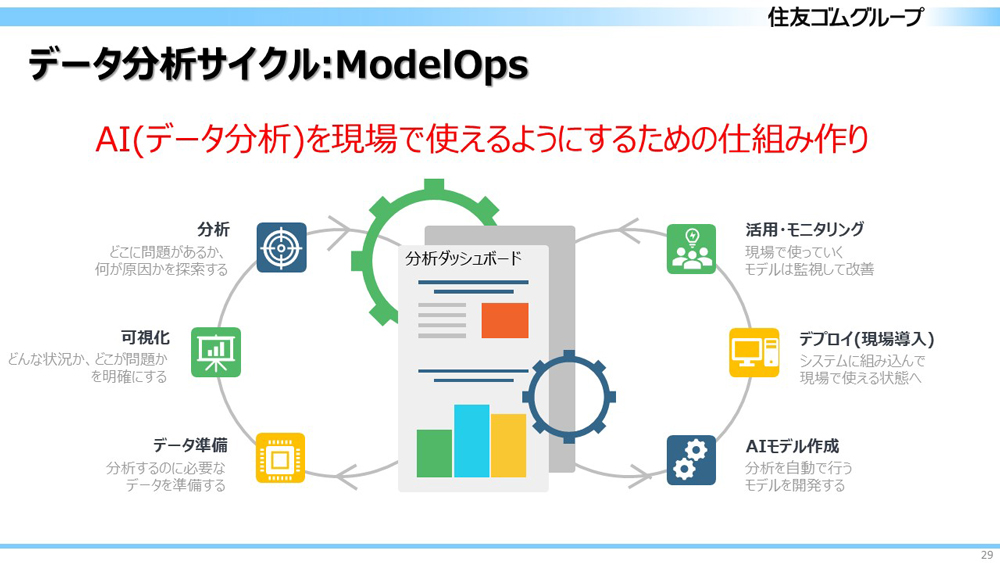
2020年11月にオンライン開催されたSAS FORUM JAPAN 2020の製造プログラムでは、「製造現場におけるデータ分析事例のご紹介とIoTプラットフォームのグローバル展開について」と題し、IoTプラットフォームを構築してグローバルに展開している住友ゴム工業の取り組みが紹介された。従来の各拠点でのバラバラなやり方ではリソースの無駄が発生しており、品質の向上や無駄の削減などに迅速に取り組むことができない。それら課題を解消するために、製造IoT推進室を新たに設立し、グローバルで統一されたIoTプラットフォームでスピード感があるデータ分析への取り組みについて解説された。
AI、IoT技術を活用し生産工程の改善を実現
1909年に創業した住友ゴム工業は1913年に自動車用の国産第一号タイヤの生産を開始し、1954年には国産初のチューブレスタイヤを、1966年にはラジアルタイヤを開発するなどで、日本のモータリゼーションに貢献してきた。現在の基幹事業はタイヤ、スポーツ、産業事業と拡がっている。
同社のタイヤ工場は国内に4つ、海外にも8工場を展開している。タイヤの製造は天然ゴムや合成ゴムを混合する工程から始まり、押出など複数の工程を経て、成型、加硫、仕上げ・検査工程の後に製品となる。「タイヤは非常に多くの工程で製造され、1つの材料のばらつきが最終の品質に大きく影響します」と言うのは、住友ゴム工業 製造IoT推進室 室長の山田清樹氏だ。課題となるばらつきを、IoTやAI技術で低減しようとしている。
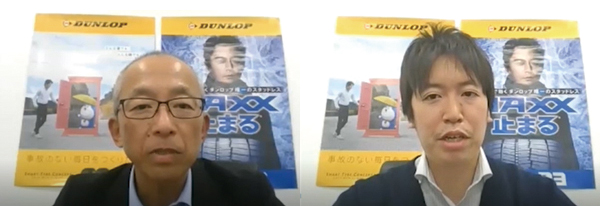
製造IoT推進室 課長代理 金子秀一氏(写真右)
住友ゴム工業では、従来は工場ごとに競争することで製造現場の改善を図り、工場間で切磋琢磨し、品質の向上やコスト削減を実現してきたのだ。この方法には弊害もあり「工場ごとに設備仕様が変わり、同じような改善を複数の工場で並行し無駄もありました」と山田氏。これでは世の中の変化スピードに遅れると考え、IoTのプラットフォームを活用し無駄を解消する取り組みを始める。
住友ゴム工業では以前から、データを活用した生産性の改善や予知保全に取り組んできた。その助走期間を経て、2017年4月に製造IoT推進室が設置された。製造IoT推進室のミッションは、ビッグデータを活用できる仕組みを構築し、生産工程の効率化に寄与すること。そしてデータを集め分析し、結果を製造現場にフィードバックすることだ。
その上で、企業としてのデータドリブン文化の醸成も、もう1つのミッションだ。従来はどうしても勘や経験に基づく意思決定となり、それを変革しデータに基づく意思決定ができる組織に変える。
改善対象の領域は、生産性、品質改善、予知保全、省エネの4つ。ロスの発生をAI、IoTの技術で見つけ、高い品質で効率的なタイヤ作りを目指す。そのために「最終的な構想としては、集中コントロールセンターを考えています」と山田氏。1ヵ所にコントロールセンターを設置し、改善する4つの領域の分析をそこで実施する。各工場からはセンターにデータを集約し、分析した結果を工場に戻す。
品質改善としては、データを分析し不良の削減を行う。生産性の改善では人の動きを分析するための映像データの収集をし、個人のスキルの見える化も行っている。設備の安定稼働では、温度、振動、停止位置など情報の分析をすることで、将来的な故障の予知などができるようにする。エネルギー消費では「まだ見える化の段階ですが、設備の稼働状態と合わせて不要なエネルギーを見つけロスを削減していきます」とも言う。
タイヤの製造原価はその多くを占める材料費のコントロールが難しいので、労務費、動力費、修繕費、仕損費などに注目して無駄を試算し金額ベースの削減目標を立てる。まずは戦略的にPoCに投資しており「ここでは効果は負わず、改善の可能性を見極めるようにしています」と山田氏。PoCの成果を現場に導入する際に、得られるであろう成果を想定し投資金額から回収年を算出、それらの値を基準にし実行に移すこととなる。
この記事は参考になりましたか?
- SAS FORUM JAPAN 2020レポート連載記事一覧
-
- 分析もクラウドの時代、「SAS Cloud」でDXを加速
- BIツールにAIを 拡張アナリティクスがもたらす分析業務の変革
- AI、IoT技術を活用し生産工程の大幅改善を実現 住友ゴム工業が実践するデータ分析事例
- この記事の著者
-
谷川 耕一(タニカワ コウイチ)
EnterpriseZine/DB Online チーフキュレーターかつてAI、エキスパートシステムが流行っていたころに、開発エンジニアとしてIT業界に。その後UNIXの専門雑誌の編集者を経て、外資系ソフトウェアベンダーの製品マーケティング、広告、広報などの業務を経験。現在はフリーランスのITジャーナリスト...
※プロフィールは、執筆時点、または直近の記事の寄稿時点での内容です
この記事は参考になりましたか?
この記事をシェア