今回はビールの話題だ。今年も残すところわずかとなり、冬の気配も濃くなってきた。暑い時期のビールもおいしいが、寒くなれば鍋料理とビール、忘年会の乾杯でビールとむしろ飲む機会は増えるかもしれない。どちらかと言えば、宴会などの最初に「気軽に味わう」のがビールだろう。しかしながらメーカーは、顧客にいかにおいしくビールを飲んでもらうか、そのためにありとあらゆる努力をしている。これは顧客が「おいしい」と感じることが、競合との戦いに勝つことにつながるからだ。
中でも日本のビールメーカー各社は、かなり鮮度にこだわりを持っている。このビールの鮮度を最適に保つために活躍しているのが、実はITの仕組みなのだ。市場の需要と供給を正確に予測し、在庫を切らさずかつ長期在庫も避けて新鮮なままビールを消費者に届ける。キリンがそのために導入したのが、最適な供給計画を立て、生産スケジューリングを行うためのアプリケーション製品「Infor Advanced Planning」と「Infor Advanced Scheduling」だった。
手組システムからグローバルなベストプラクティスを持つアプリケーションへ
キリンビールでは、ビールと低アルコール飲料類など150種類以上の製品を提供している。そんなキリンでは、これまではレガシーな独自の手組システムでビールの需給計画(製造出荷計画)を立案していた。「最適化のエンジンは自分たちの手で構築したものでした。その仕組みを長い間使ってきたのですが、得られる結果が本当に最適かどうかの検証ができませんでした」と言うのは、キリンビジネスシステム株式会社 開発プロジェクト統轄部 システム開発グループ 部長(当時)の前田賢司氏だ。過去からの経験上、出てくる答えは間違いではないはずだが、それが「最も適したもの」かどうかは検証しようがなかったのだ。
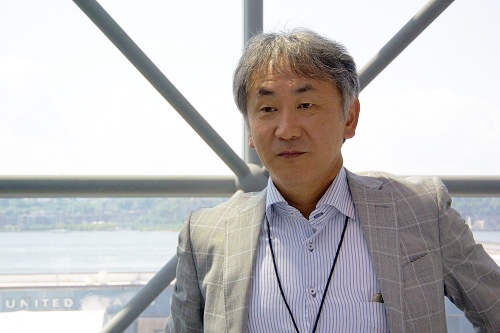
開発プロジェクト統轄部 システム開発グループ 部長(当時)
前田賢司氏
またレガシーなシステムでは、運用メンテナンスのコストが課題であり、システムの老朽化もありこのままずっとこの仕組みを使い続ける訳にもいかない。「どこかのタイミングで、入れ替える必要がありました。仮にこのまま使い続けるとなれば、いつかは大きく手を入れる必要が出てきます。それには莫大なコストがかかるので、それも考慮し5年で投資コストが回収できることを目標に新たなシステムへの移行計画を立てました」と前田氏。
新たに採用するシステムは自分たちの手で最適化エンジンを作るのではなく、市場で評価されているベストプラクティスを採用することにした。そのためにいくつかのアプリケーション製品を比較し、最終的に選んだのはInforの製品だった。キリンでは得られる計画の正確性を一番に求めていた。そのような要件がある中で「Inforは最適化エンジンが一番しっかりしていたことが採用の理由です」と前田氏。もう1つの採用理由は、計画の最適化モデルを作るにあたって説明変数を入力することになるが、その説明変数をどれだけ柔軟に数多く扱えるかもポイントだった。
「Inforの計画機能は、パッケージ製品と言うよりもモデルを作るソフトウェアです。パラメータを組み合わせてモデルを作ることができ、社内ではこれをレゴのようなものだと表現しています。これは、パッケージ製品で自社のやり方に合わせカスタマイズが必要になると言うのとはちょっと違います」(前田氏)
評価した結果、Infor製品の印象は最適化エンジンがしっかりしていたと前田氏は言う。これはグローバルのビールメーカーのほとんどが、Inforの製品を採用していることでも証明されているとのこと。そのためビールメーカーのベストプラクティスが入っており、さらにパッケージのタイムリーなバージョンアップで最適化が維持され続けることも期待できる。
実際に使い始めてパラメータの設定のしやすさが、旧来の手組のシステムと大きく違うとも言う。以前の仕組みではコーディングが必要な部分もあり、専門家でなければ設定できないものもあった。対してInforの仕組みは、現場のユーザーが設定できる。「当初は本当に現場でできるか不安もありましたが、プロジェクトが進んでいくとユーザー部門の人たちは自分で設定できるようになっていました」と前田氏。
またパッケージを採用するに当たっては、パフォーマンスの要件もあった。モデルの実行時間で30分以内、できれば20分で処理を済ませたかったのだ。
「20分という時間にこだわったのは、システム的な制約ではなく業務プロセスからの制約です。今回は、システムの入れ替えと同時にビジネスプロセスの再設計もしたのですが、1日の一連の業務プロセスを設計したら、1回の処理を20分で実行することが業務上の必須条件となっていたのです」(前田氏)
データ量が多く計算の複雑さもあるので、時間がかかる処理も発生する。配送ルートの数などが多い場合は、どうしても最適化の計算の時間が長くなる。旧システムでは1時間以上かかっていた場合もあったが、Inforに移行しチューニングを施した結果、Advanced Planningの処理は要求通り20分程度に収まるようになったのだ。
この記事は参考になりましたか?
- この記事の著者
-
谷川 耕一(タニカワ コウイチ)
EnterpriseZine/DB Online チーフキュレーターかつてAI、エキスパートシステムが流行っていたころに、開発エンジニアとしてIT業界に。その後UNIXの専門雑誌の編集者を経て、外資系ソフトウェアベンダーの製品マーケティング、広告、広報などの業務を経験。現在はフリーランスのITジャーナリスト...
※プロフィールは、執筆時点、または直近の記事の寄稿時点での内容です
この記事は参考になりましたか?
この記事をシェア