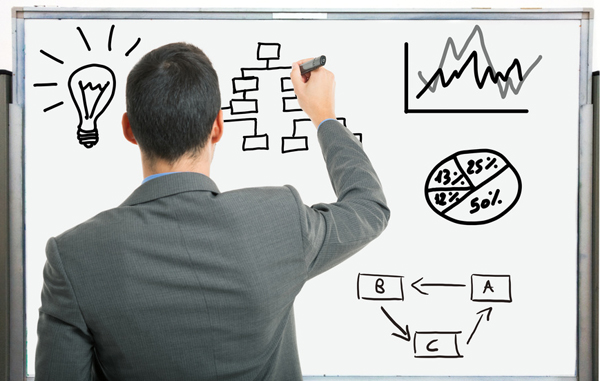
「情報システム部門はコストセンターである」。これがこれまでの常識でした。しかし、大量データ分析の基盤が手の届くものとなった今、データ分析の結果を外部提供することによって情報システム部門はプロフィットセンターにもなり得ます。データ分析の基盤を貸す、という方法もあるかもしれません。今、データマネジメントを支える要素技術の進歩がビジネスの姿を大きく変えようとしています。
改善プロセスの考え方を見直す
日本においてはビジネスにおける改善といえばPDCAサイクル(計画[Plan]- 実行[Do]- 評価[Check]- 改善[Act]の サイクルを繰り返すことによって、業務の継続的改善を実現する)があまりに有名であると同時に、最も重視されていると言っても過言ではないでしょう。データ利活用はほとんどの場合、何かの改善に利用されるのが自明ですから、まずは改善プロセスの考え方について見直してみます。
PDCAサイクルの適用では、いかにサイクルを高速に回すかということに重きが置かれています。PDCAサイクルでは、過去行動のフィードバックによって計画策定を行うため、実行した後、評価の時に至ってからようやく現場からのフィードバックを得て、アクションを取ることになるためです。当初計画の段階で現場と乖離していたならば、計画の転換が必要であり、それには労力だけでなく、多くの時間が必要となるのです。
つまり、常に計画が前提にあり、現場における内外環境の情勢判断をする過程が手薄になっているため、サイクルを回している間に、想定外の致命的な事態に至るリスクがPDCAサイクルにはあるのです。
現場が刻々と変わっていく状況に対応するためには、結局のところ、データ分析の力を用いてこのサイクルを極限まで高速化することを一つの目標に設定することがあります。しかし、どんなに高速にこのサイクルを回そうとも、カタストロフィを避けられなかった例もまた枚挙にいとまがありません。
評価の過程で、たとえ変化の潮目に気づいても、それが何か、なぜ起こったのかを見極め、納得しないと行動に移れないことが往々にしてあるからです。このため高度なデータ分析、ついにはAIを用いてシンキングタイムをゼロにすることを試みるにとどまらず、PDCAサイクルをシュミレーションする事例もでてきているのが現状です。
一方、データ分析をより積極的に利用することを模索するうちにPDCAサイクルを捨て、米軍をはじめ、広く機略戦コンセプトの中核的な理論として受け入れられているOODAループ(監視[Observe]- 情勢判断[Orient]- 意思決定[Decide]- 行動[Act]のサイクルを繰り返すことによって、適格な意思決定を実現する) に従うことを決める例も出てきています。
監視により情勢変化の気づきを得ること、情勢判断による情勢変化の意味がわかること、この2つによって行動を起こすことが容易になります。予測外のこと、期待していなかったこと、といった想定外のことに対して、最速で意味づけすることで、意思決定と行動を迅速に行うことができるのです。
OODAループでは何よりPDCAサイクルの欠点であった現場との乖離を最初から含みません。現場を起点とするため、実行時には現場の置かれた状況がはるか先に行っているといったこともありません。
これらのことから、リアルタイムで多量のデータを処理できるようになった利点を最大限活かすために、PDCAを捨てOODAを採用する例が出てきているわけです。もちろんこのサイクルにもリスクがないわけではなく、OO-OO-OOスタックと呼ばれるDに移れない事態が想定されます。各個人の意思決定は各々異なっているだけでなく、的確に動作することを保証されるものではないこと、 組織においては複数意思決定のコンフリクトを生じやすいことがその要因になります。
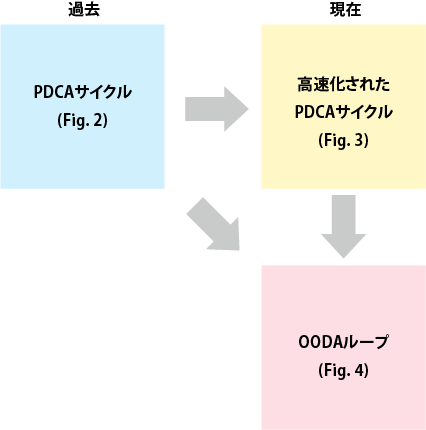
Fig. 1 ビジネスプロセスにおけるデータ分析の適用
この記事は参考になりましたか?
- 戦略的データマネジメント講座連載記事一覧
-
- 小手先のワードに振り回されるな!10年後も戦える企業であるために【戦略的データマネジメント...
- PDCAサイクルからOODAループへ!改善プロセスの考え方を見直そう【戦略的データマネジメ...
- 無駄なIT投資していない? データ分析基盤構築とツール導入の要諦【戦略的データマネジメント...
- この記事の著者
-
藤田 泰嗣(フジタ タイシ)
PwCコンサルティング合同会社 ディレクター
ビジネスとテクノロジを接続するテクノロジ領域のクラッチコンサルタントとしてアーキテクチャに関する経験を多数有する。ビジネステーマはTrustworthy DATA。 情報システム担当部門の業務改革を基軸に、データガバナンス改革、ワークスタイル改革などを手掛...※プロフィールは、執筆時点、または直近の記事の寄稿時点での内容です
この記事は参考になりましたか?
この記事をシェア